Lager betong nesten uten CO2-utslipp
Betong er verdens mest brukte materiale etter vann og står for seks til åtte prosent av verdens CO2-utslipp. Nå kan en Stavanger- oppfinnelse kutte utslippene med opptil 90 prosent basert på avgangsmasser fra gruveindustrien.
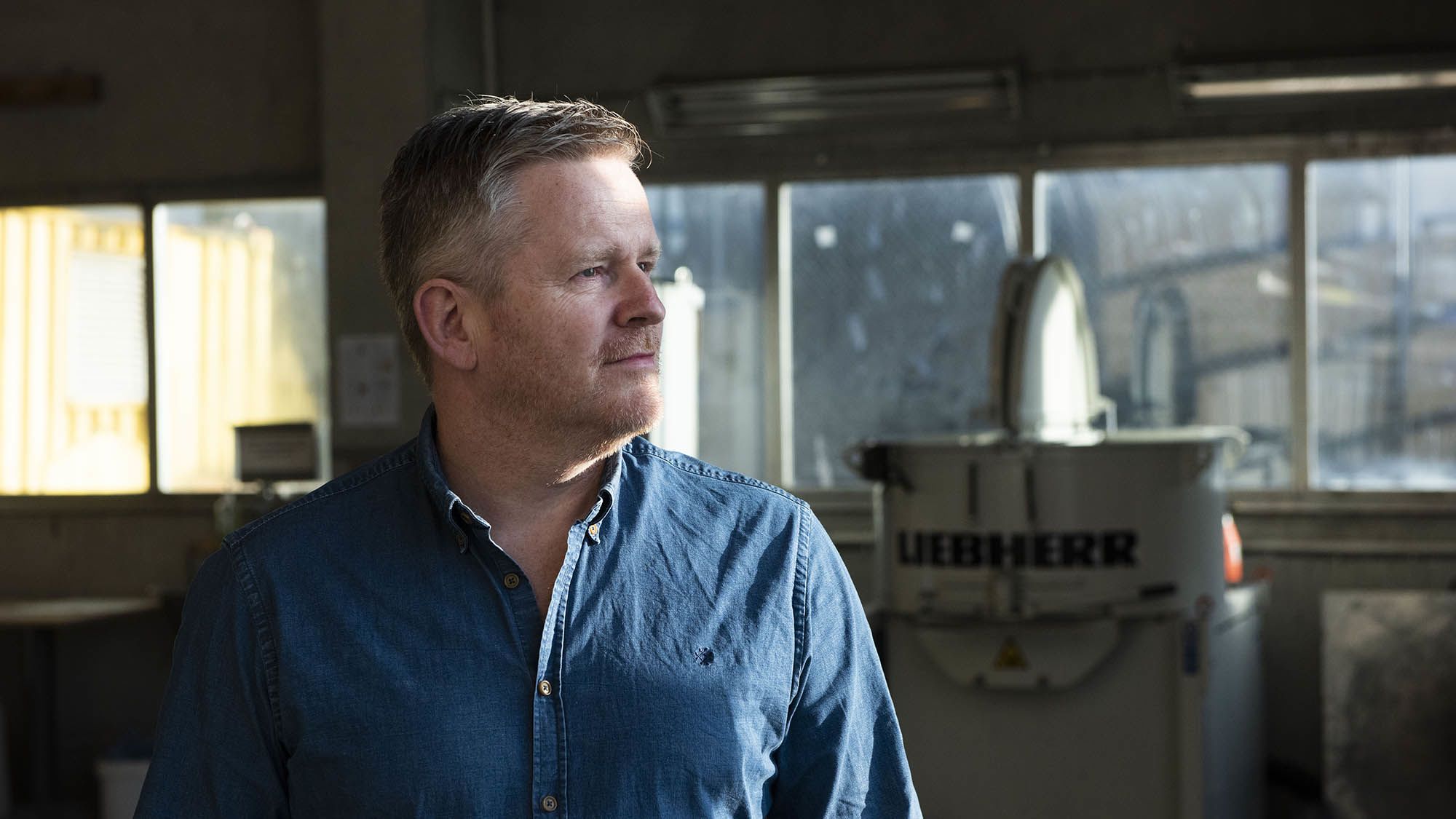
I en hall på Sola står en Kenwood kjøkkenmaskin og sviver. Oppi bollen som normalt gjerne ville inneholdt
egg, mel og sukker, er det helt andre ingredienser som blandes. Her heller Ida Marie Gabrielsen i vann, sand og geopolymer-sement som røres rundt til det blir en jevn røre, som til forveksling ser helt lik ut som vanlig betong.
– Målet er å lage en blanding som ser og oppfører seg helt likt som vanlig betong, og det gjør det. Når denne har fått rett konsistens så heller jeg oppi formen og setter til herding, forklarer Gabrielsen som jobber som forsker i Saferock.
Lavere CO2-utslipp
Bruker du Google og søker opp geopoymer får du nærmere én million treff, men akkurat denne spesielle bruken av geopolymer er det få eller ingen i verden som driver med. I 2012 begynte Mahmoud Khalifeh forskningen på området sammen med Helge Hodne ved Universitetet i Stavanger, til bruk som pluggemateriale i olje- og gassindustrien. Nå kan det revolusjonere bygg- og anleggsbransjen.
– Saferock ønsker å lage bærekraftige produkter for fremtidens bygg og anlegg, og for oss handler det om betongrelaterte bygningsmaterialer, forklarer daglig leder Espen Lea.
Verden bruker enorme mengder betong, og faktisk er betong verdens mest brukte materiale etter vann. Millioner på millioner tonn med betong bruker store mengder sement som er ansvarlig for seks til åtte prosent av verdens CO2-utslipp. Gjenbruk av masser fra gruveindustrien kan males til et fint pulver og blandes til det selskapet kaller geopolymer-sement.
– Lab-tester viser at dette fungerer og vi lager produkter som har lavere CO2-avtrykk og som tåler varme og kjemikalieangrep bedre enn tradisjonell betong, sier han.
Han har vært med fra starten av og så tidlig mulighetene som finnes innen bygg- og anleggsbransjen. Selskapet har sikret seg eksklusive lisensrettigheter til bruk av disse patentene som UiS har tatt på denne geopolymer-teknologien.
– På to år har vi ti ansatte, og en veldig god miks av unge fremadstormende og flinke erfarne folk, og jeg har stor tro på at dette må vi gjøre i samarbeid mellom oss og universitetet, sier Lea.
Pilotfabrikk
Selv om labtestene ser veldig bra ut og selskapet er sikre på at deres produkt fungerer, er Lea klar på at teknologien ikke er perfekt på alle områder per dags dato.
– Sement og betong har hatt en teknologisk utvikling gjennom 200 år, mens for geopolymer har ikke utviklingen pågått så lenge. Svakhetene som finnes i dag mener vi det er mulig å fikse, vi trenger bare litt mer tid, mener Lea.
Første steg for å verifisere teknologien vil være å bygge en pilotfabrikk som etter planen skal stå klar neste sommer. Da vil også selskapet kunne selge produktet og få en omsetning. Akkurat nå venter de svar fra Enova på en søknad om støtte til pilotfabrikken. Dialogen er god og de håper på et svar før jul.
– For oss hadde det vært en flott julegave å fått Enova med på dette. En sånn fabrikk vil kreve 25 millioner i investeringer, der Enova kan gå inn med inntil 45 prosent, sier den daglige lederen.
På fabrikken skal masene males ned til et veldig fint pulver og så blandes til et homogent pulver - geopolymer-sement. Dette må gjøres med rett kvalitet.
– Dermed får vi både verifisert at dette kan oppskaleres og fungere samtidig som vi får demonstrert produktet og får noen referanseprosjekter der vår type betong blir brukt.
Men akkurat her ligger også et av de største hinderne akkurat nå: De internasjonale betongstandardene krever et visst innhold av OPC (Ordinary Portland Cement), tradisjonell sement for å kunne brukes. Håpet er at inntil regelverket endres, så kan produktet brukes til ikke-bærende konstruksjoner.
– Akkurat her finnes det en del andre ting betong brukes til, og gulv i parkeringshus mot grunn eller støttemurer går det nok an å få unntak fra kravene, forklarer Lea og fortsetter:
– Dagens regelverk er ikke tilpasset vårt materiale og er dermed et hinder for at bygg- og anleggsbransjen kan redusere sine CO2-utslipp.
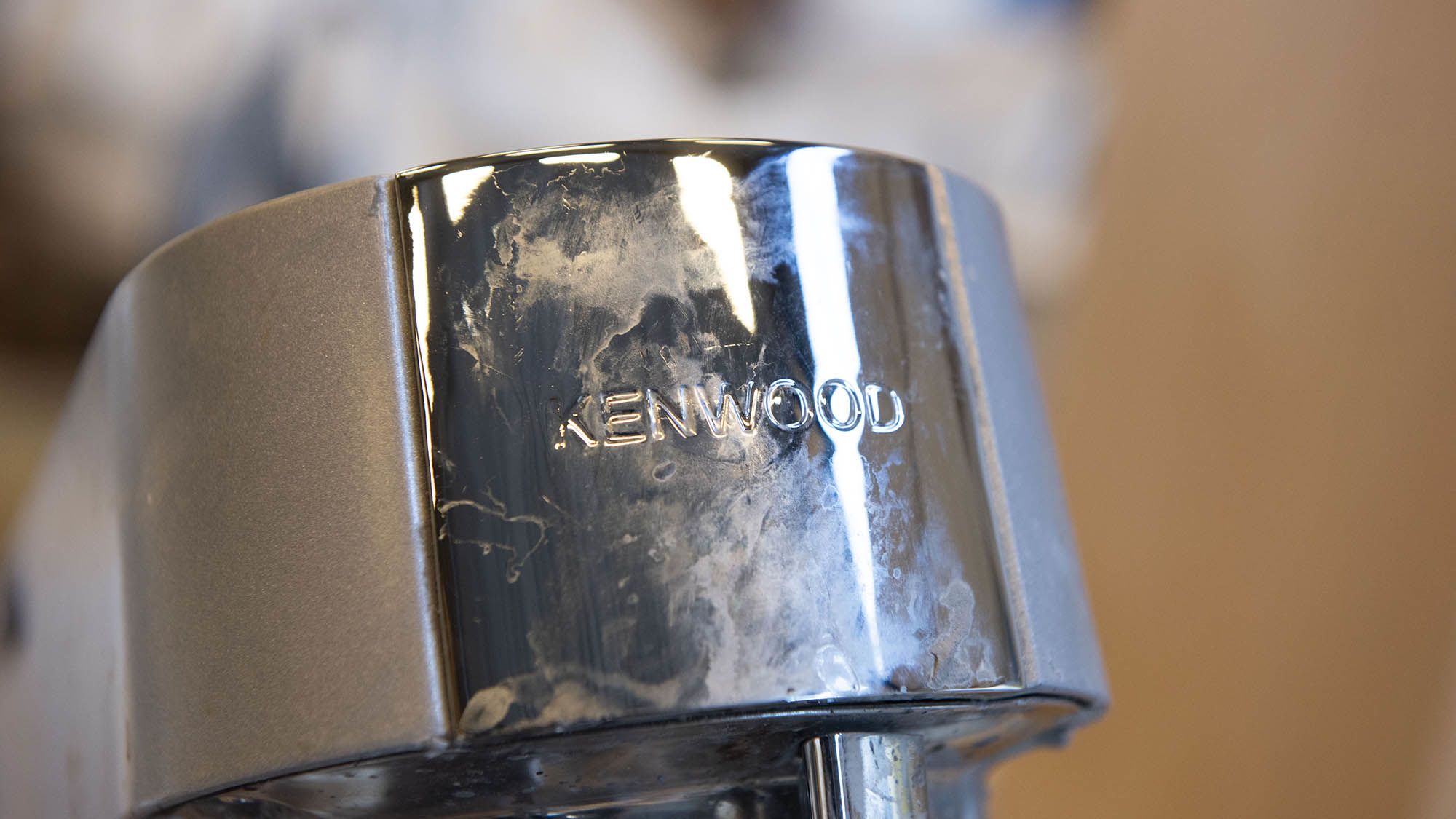
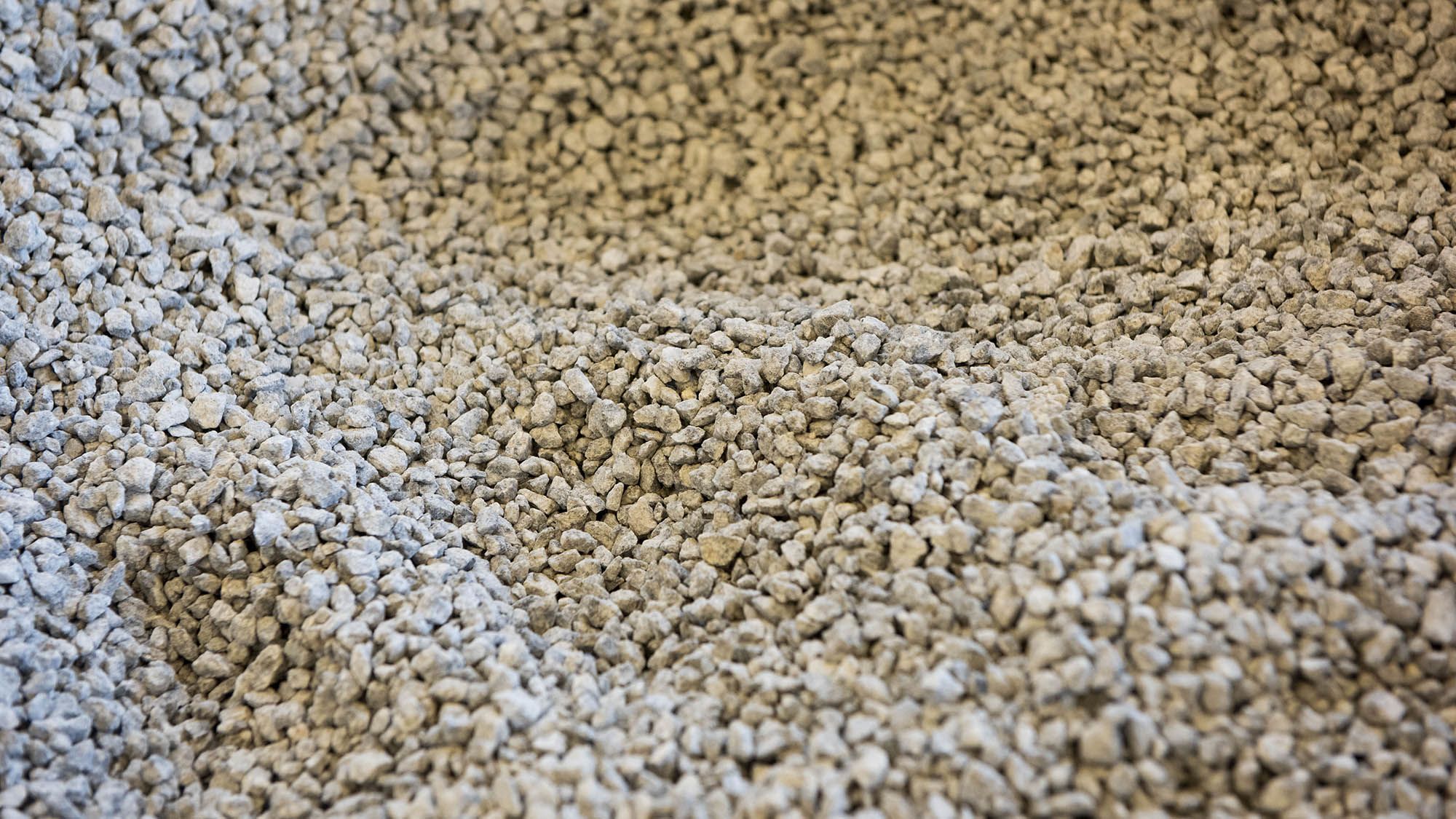
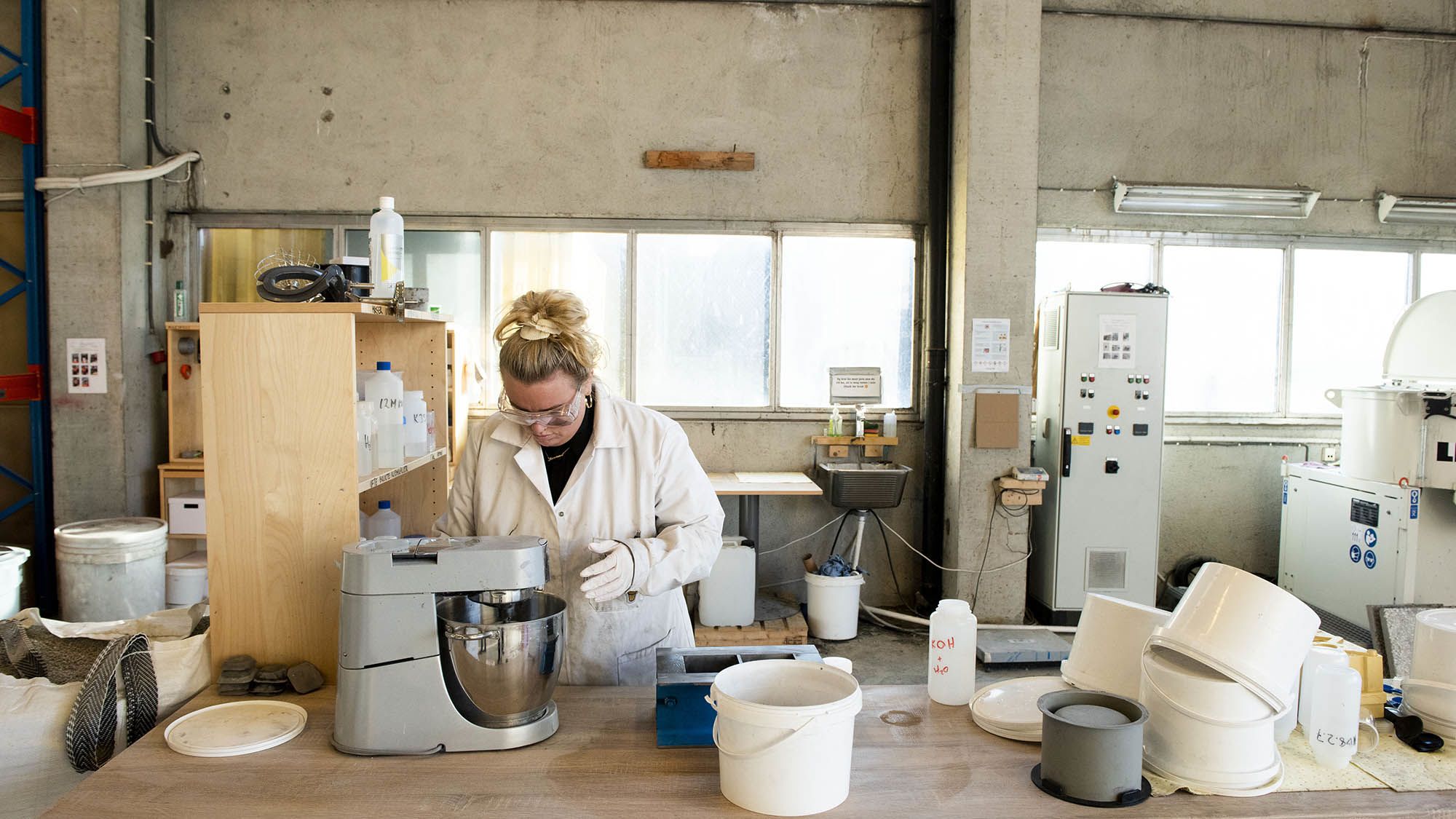
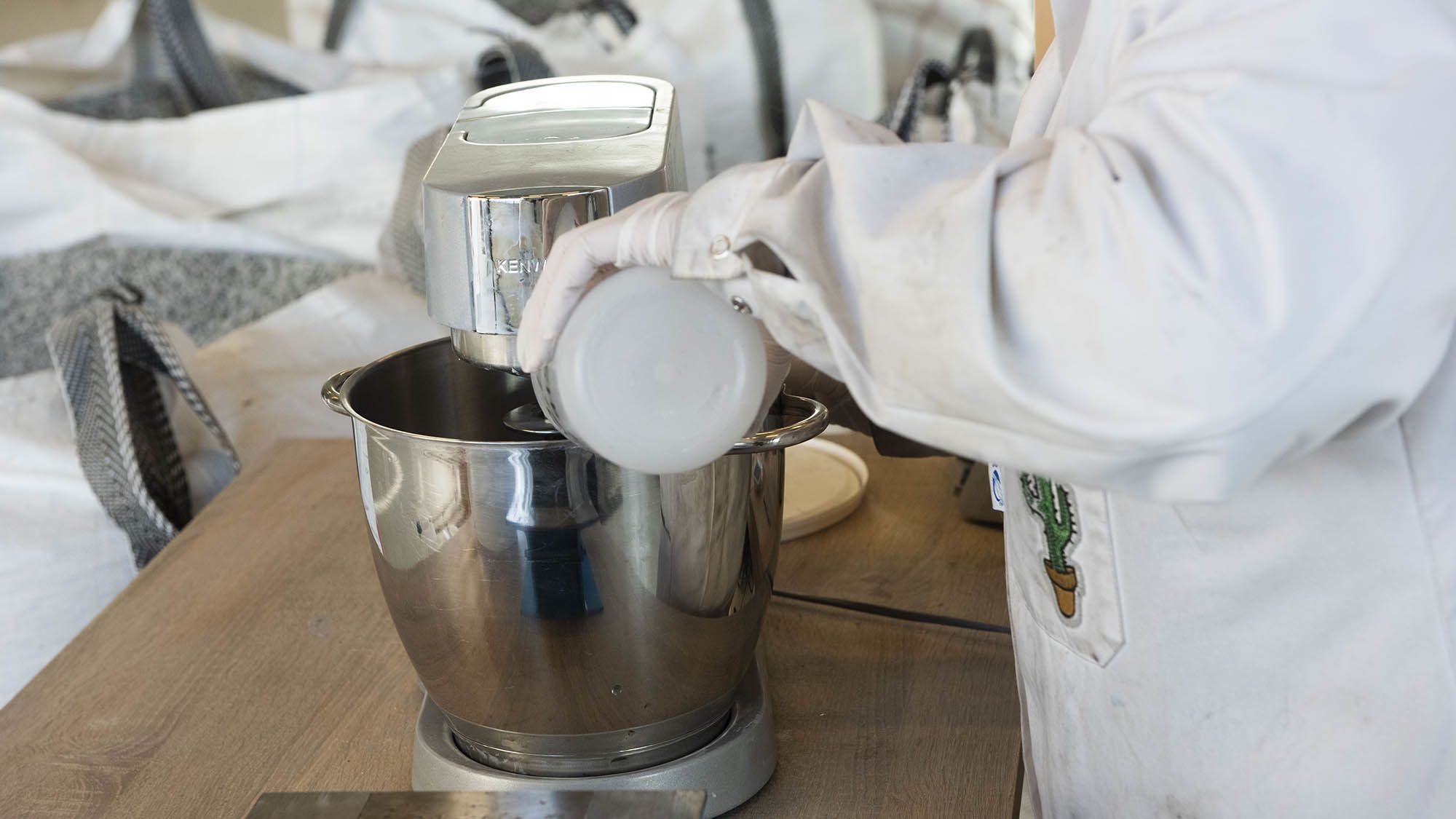
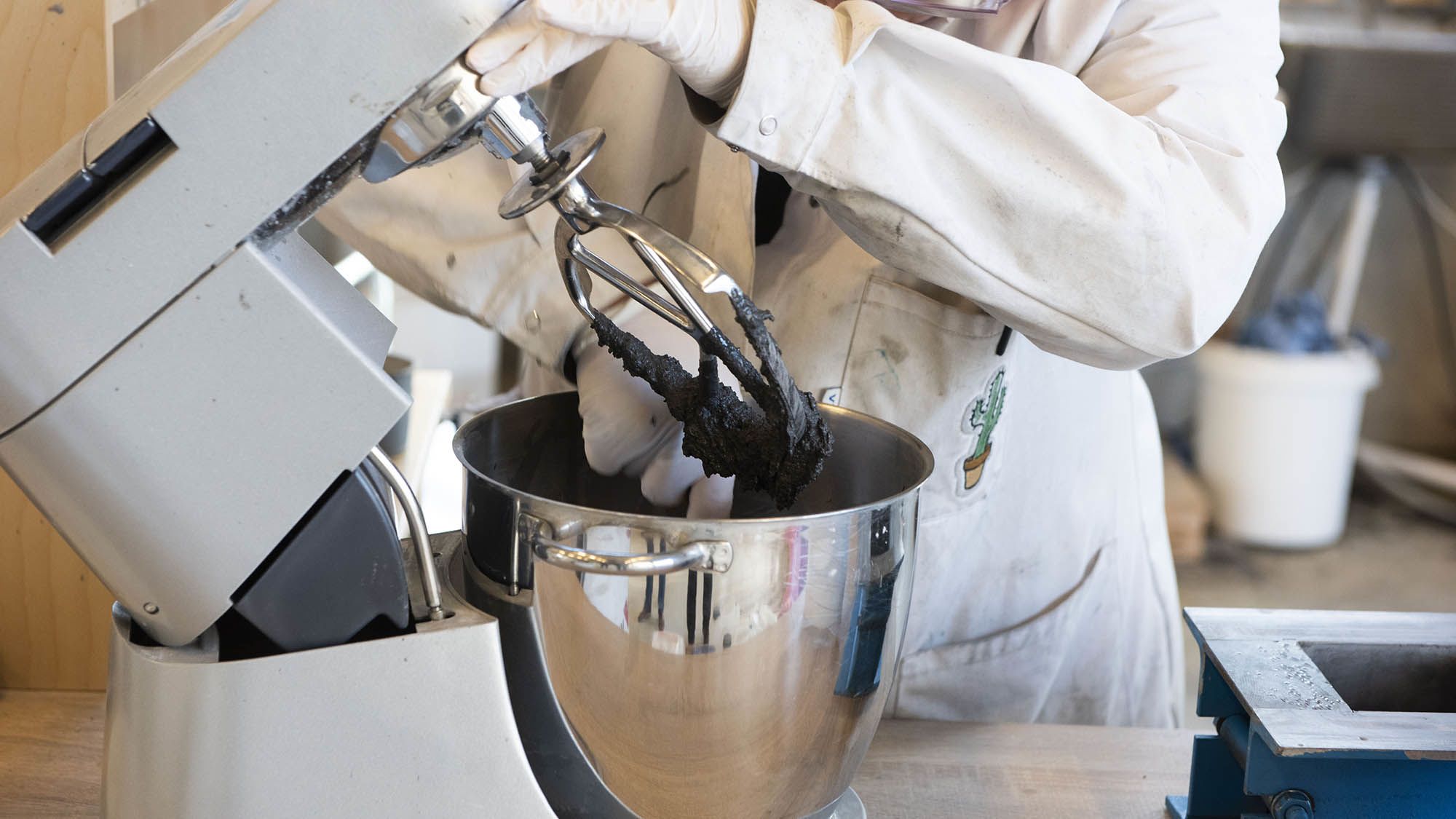
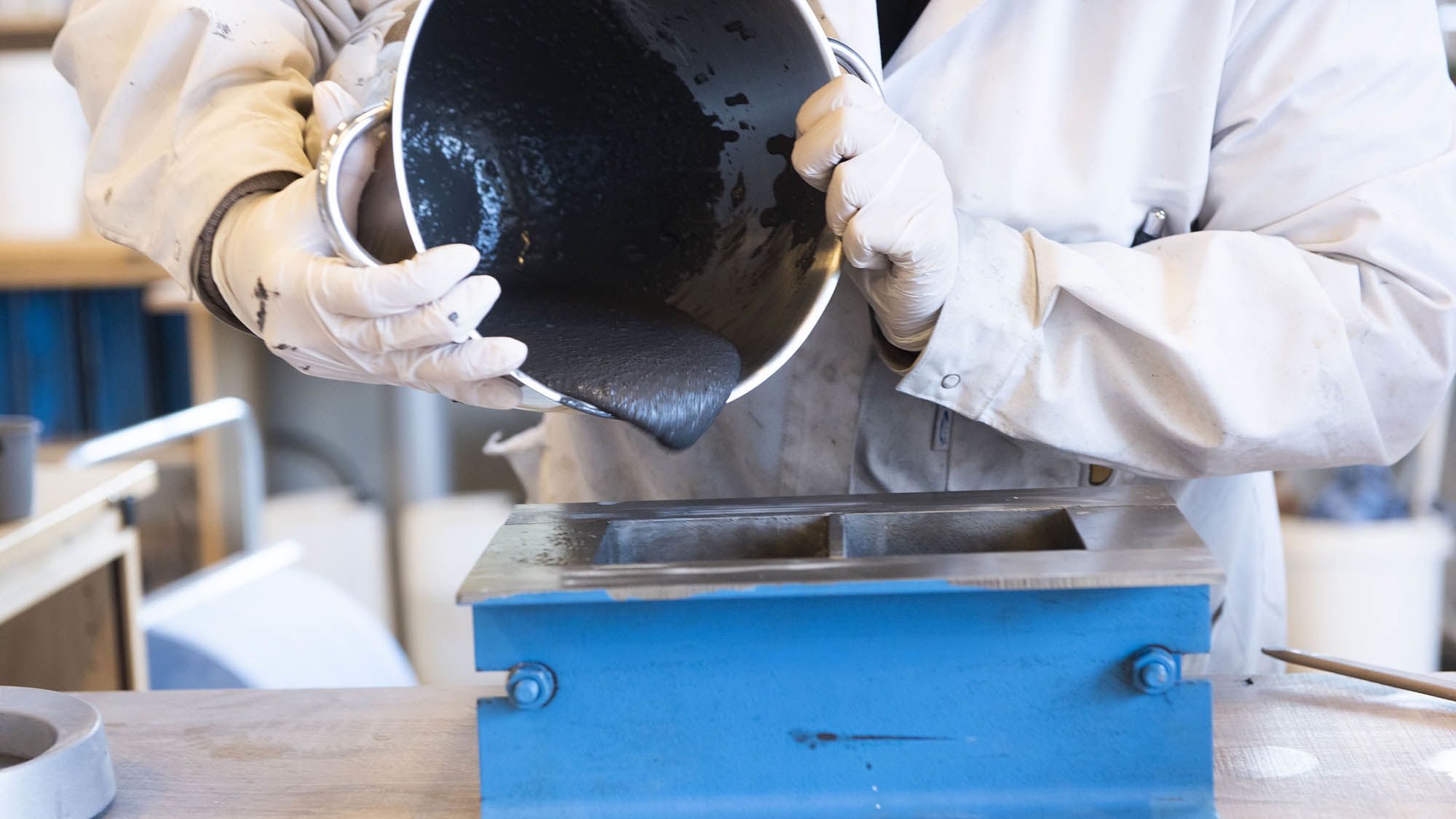
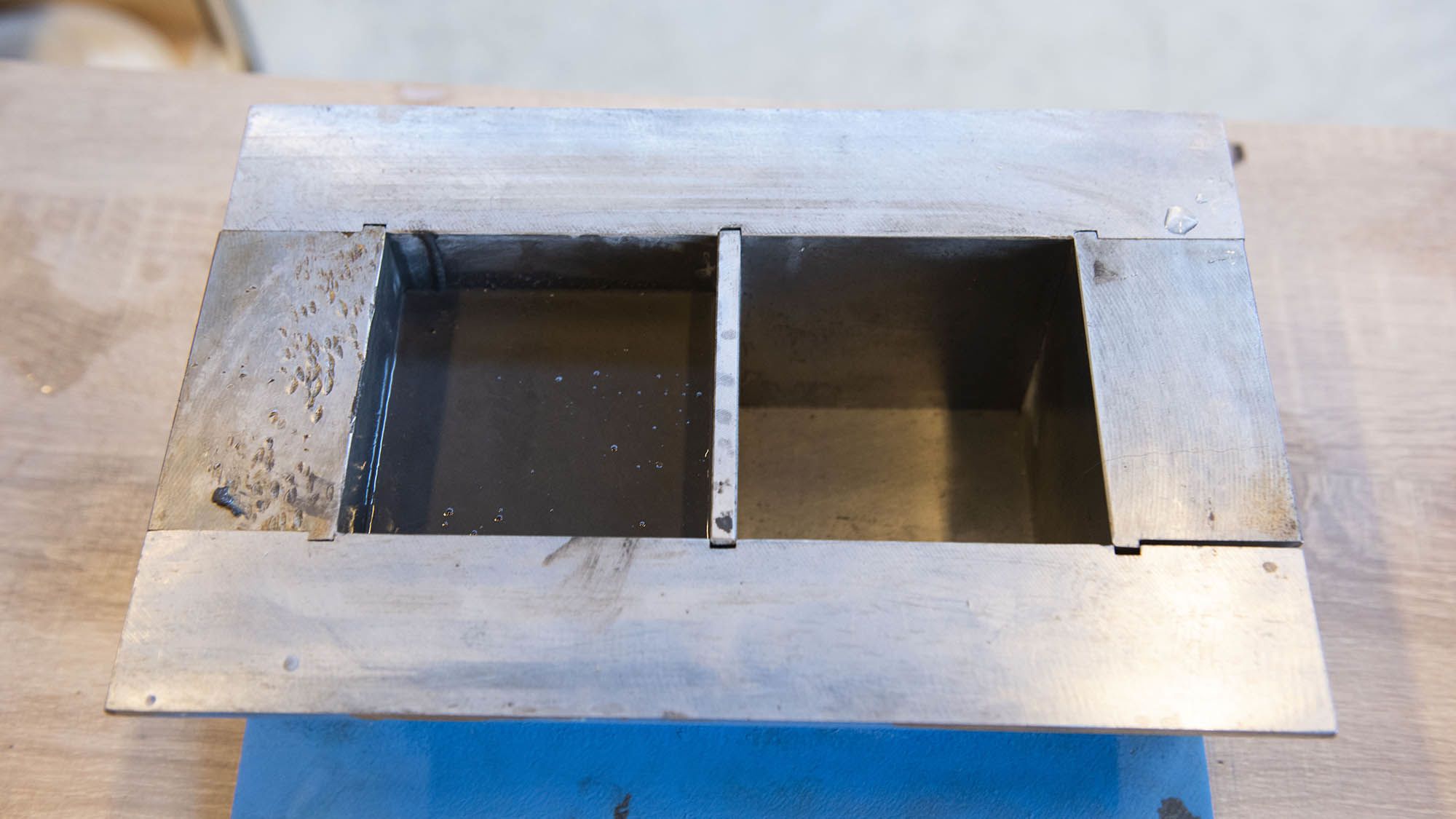
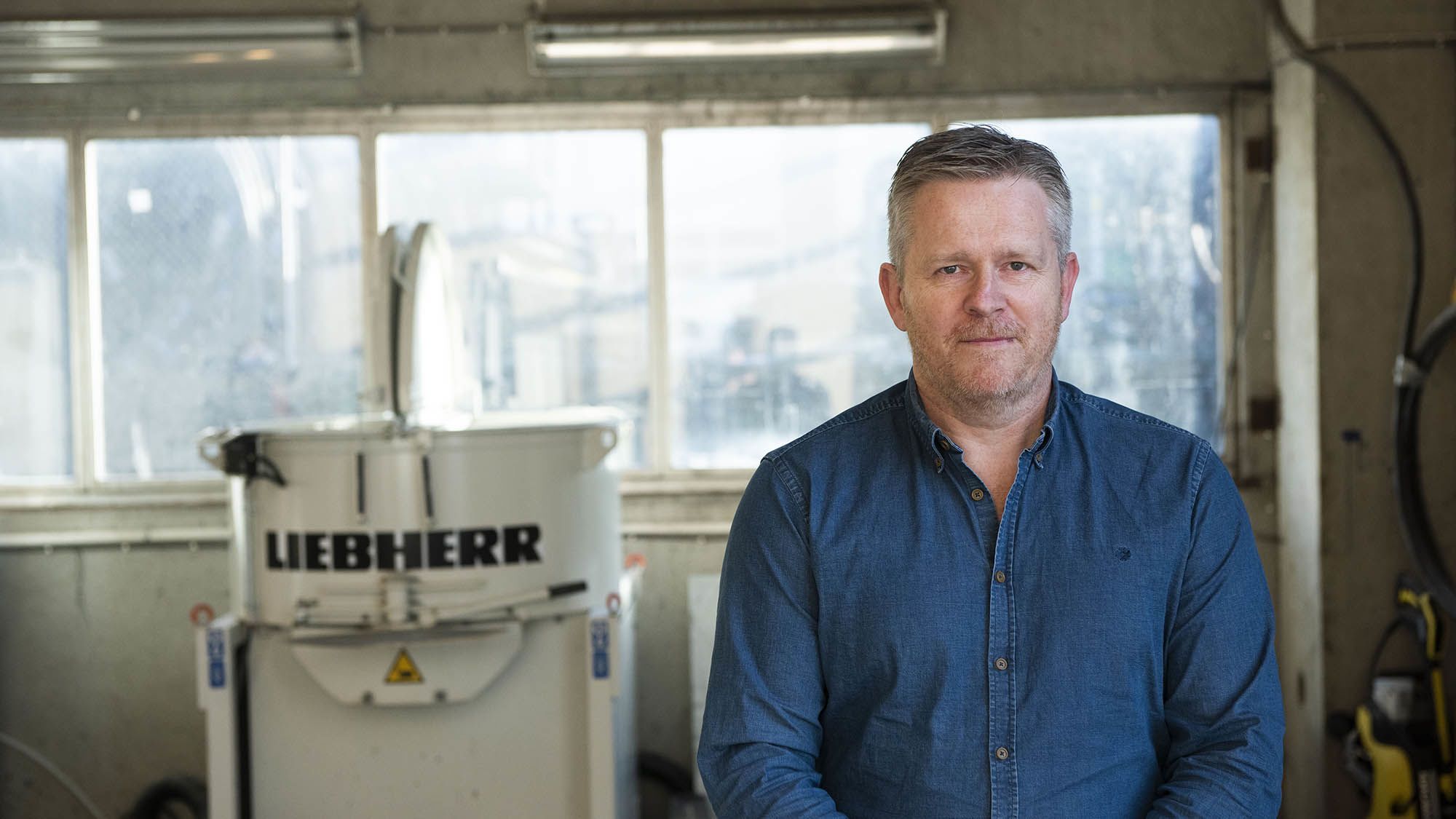
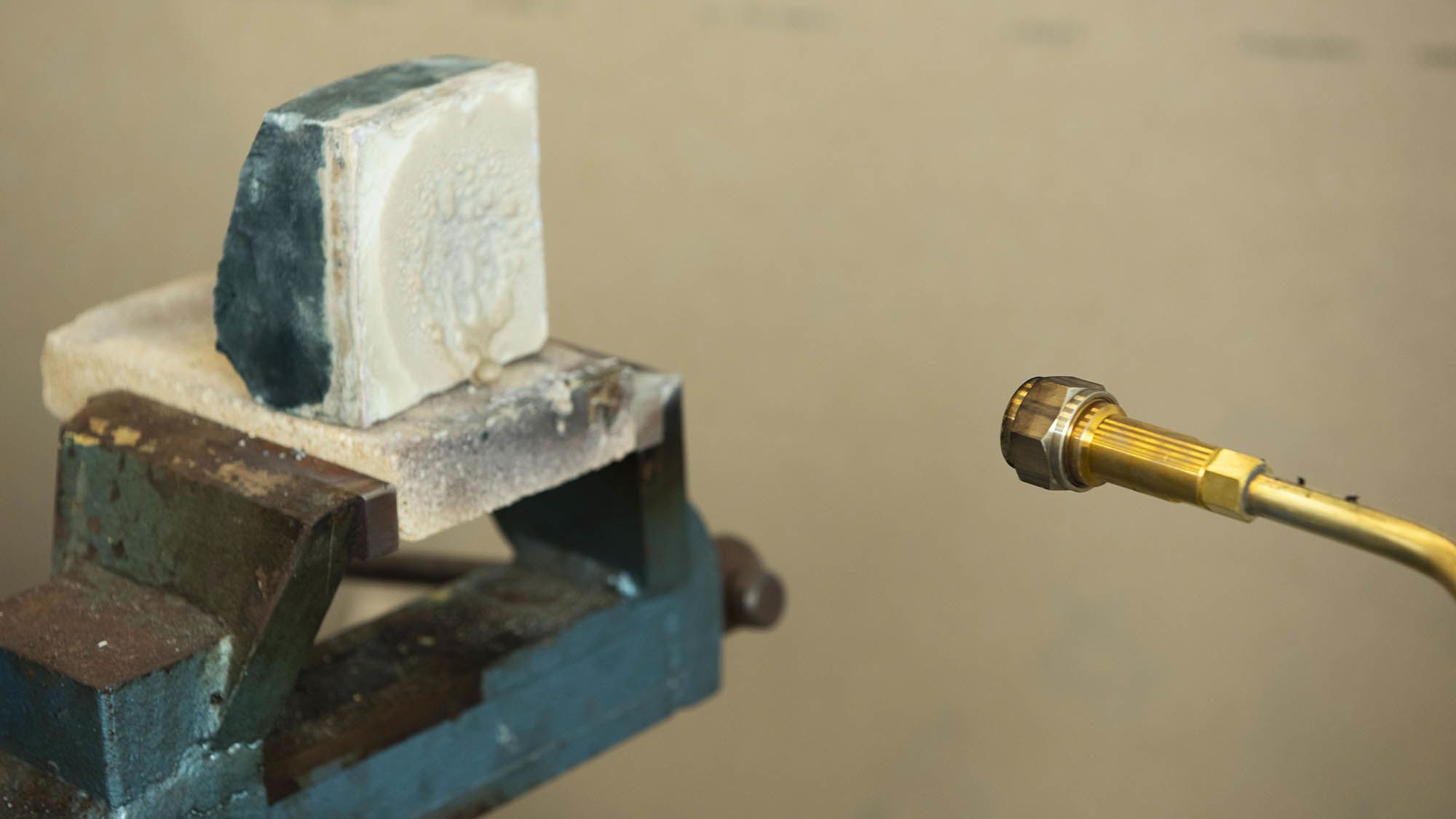
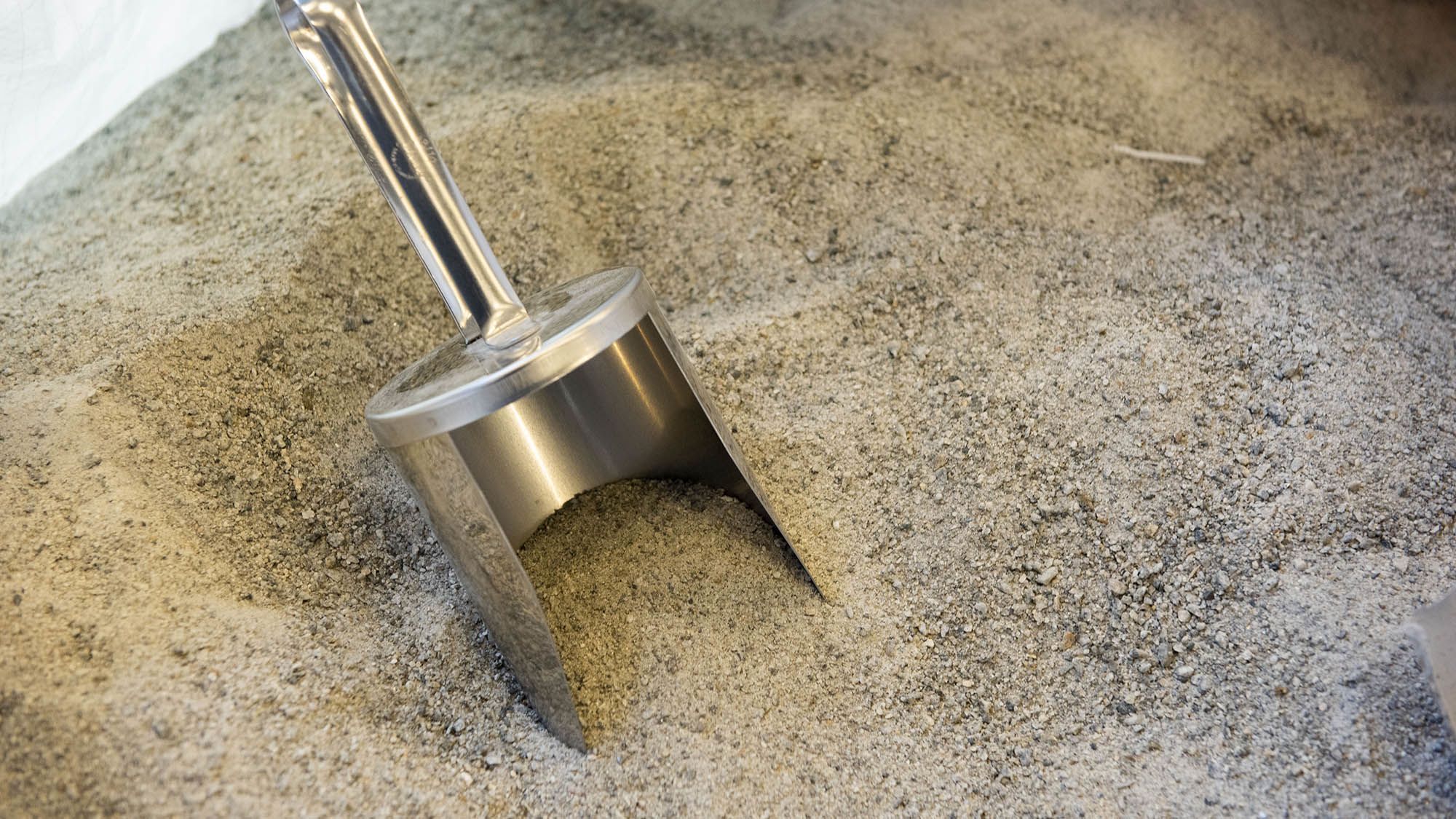
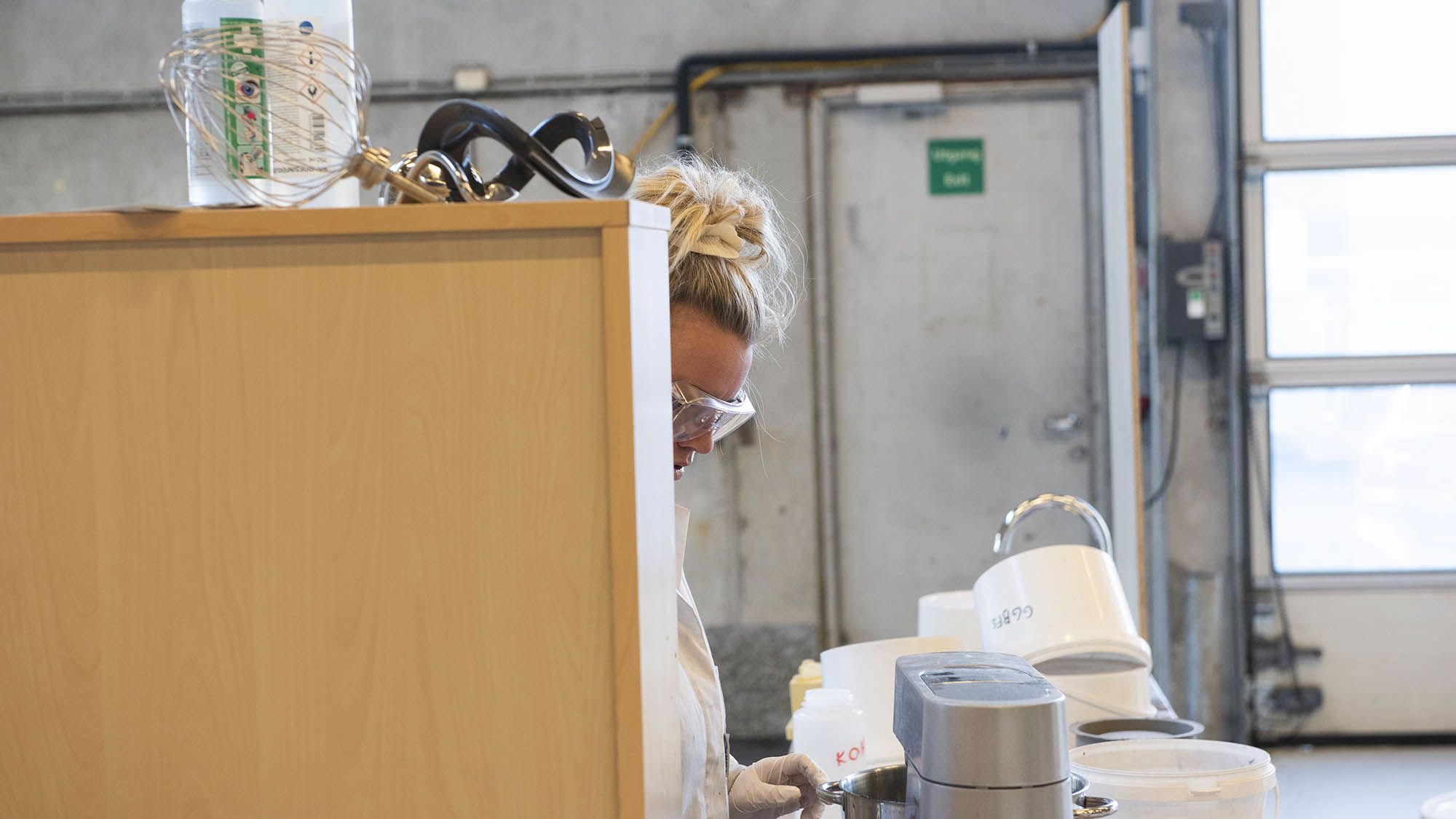
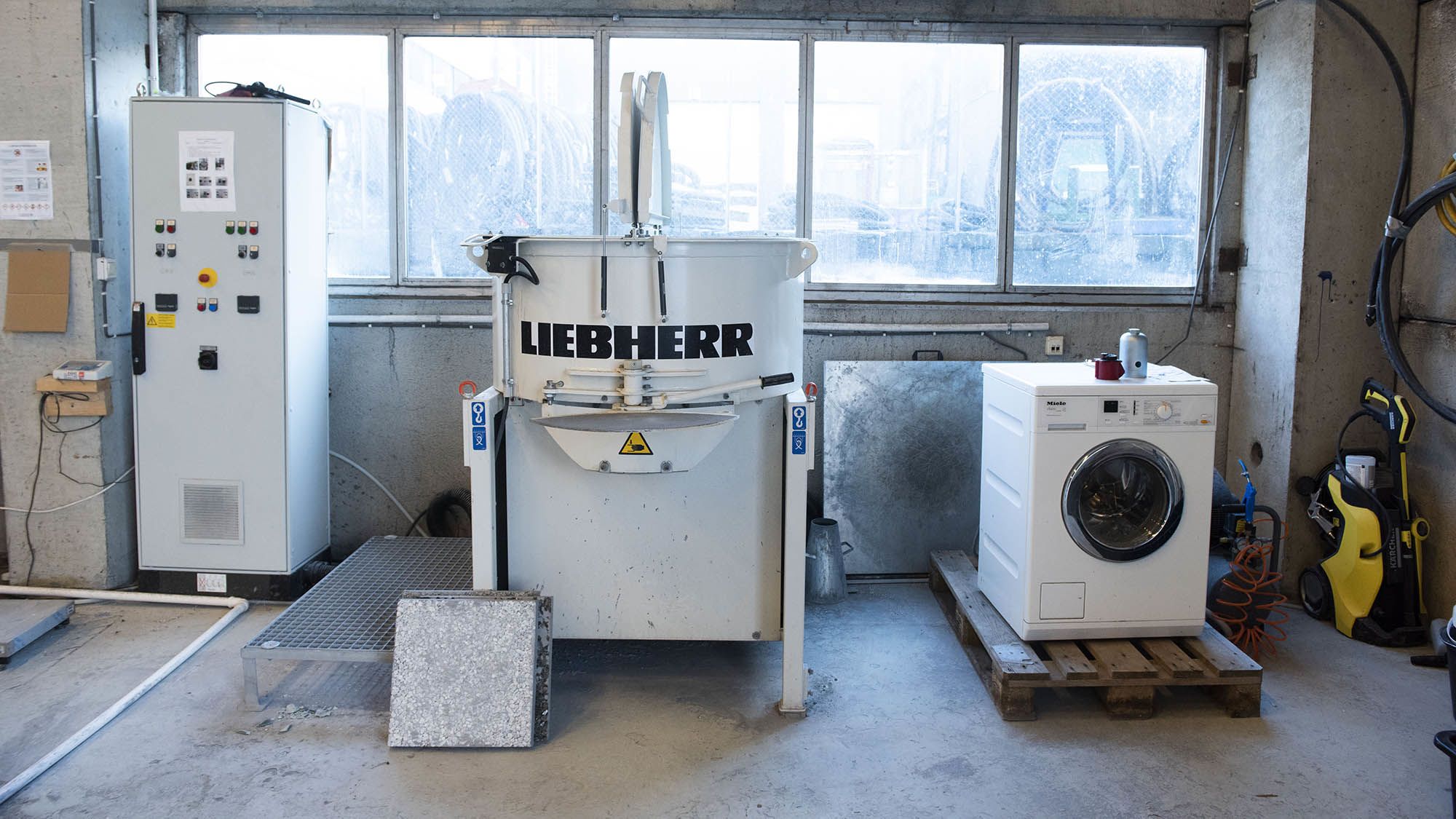
Avfall til ressurs
Ute i hallen har betongmassen blitt fin og jevn. Gabrielsen får betongen over i en liten kvadratisk form som settes til herding. Inne i et lite rom står hylle på hylle med slike prøver, som testes mot varme og kjemikalier. Mens vanlig betong kun tåler lave temperaturer opp mot 400-500 grader, skal Saferocks betong tåle opp til 1200 grader. Dette testes i samme hall der de så betongkubene utsettes for ekstrem varme.
– Egenskapene er altså bedre med denne type betong, sier Lea.
Geopolymer-sementen slik den er i dag vil gi 70-80 prosent mindre CO2-utstlipp sammenlignet med bransjestandarden for betong. I tillegg jobber Saferock med en teknologi for å binde CO2 i betongen, slik at det materialet også blir et karbonfangst- og lagringsprodukt.
– Ved å gjøre CO2 om til et fast stoff og ikke la det forsvinne ut av produktet over tid vil vi faktisk redusere utslippene med 80-90 prosent. Det er betydelige mengder CO2 på verdensbasis!
Siden Saferock bruker avgangsmasser fra gruveindustrien med en sirkulær tankegang, gjør man et problemområde i den industrien til en ressurs.
– Vi gjenvinner avfall til en ressurs. I dag samarbeider de med Titania, men ser også for seg at de bruker andre kilder som råstoff fra andre gruveprosjekter i Norge.
I fremtiden vil produksjon ligge tilknyttet gruveprosjekter for å gjøre råstoffet så kortreist som mulig. Målet er å ha flere produksjonsfasiliteter i Norge innen syv år.
– Blir pilotfabrikken en suksess så bør vi få til dette, og ha geopolymer-sement for salg i Norge og eksport til utlandet, forklarer Lea.
Har et ansvar
Han kjenner heller ikke til noen direkte konkurrenter i Norge. Noen finnes i utlandet, men de har ikke helt samme konsept og er avhengige av flyveaske, et avfallsprodukt fra kullkraftverk. Flyveaske brukes i betongindustrien for å erstatte CO2 og redusere fotavtrykket.
– Men det kommer som et restprodukt fra kullkraftverk som egentlig skal fases ned. Flyveaske er derfor et problem i dag og vil være enda vanskeligere å få tak i fremtiden.
En annen effekt av en suksess av pilotprosjektet vil være flere arbeidsplasser. Målet er å være 20 ansatte om ett år, altså en dobling fra i dag. Tilgangen på kompetanse er derimot begrenset i denne bransjen, og selskapet søker også internasjonalt.
– For å få suksess er vi nødt til å rekruttere de beste folkene. Finner vi dem her lokalt er det supert, men vi må se overalt. Akkurat nå har vi tre ledige stillinger og oppfordrer alle som synes vi høres spennende ut til å søke.
Kompetansen de søker etter handler om erfaring med geopolymer, folk med kjemibakgrunn, sterk bakgrunn innen sement og betong, kandidater som har drevet med utvikling av ildfast materiale, noen som er sterke på materialteknologi.
– Erfaring med geopolymer finnes det veldig lite av i Norge, erkjenner Lea.
– Hvor vil dere bygge pilotfabrikken?
– Akkurat det jobber vi med nå. Er i dialog med noen aktører, samtidig som vi har et prosjekteringsfirma som skal få en oversikt over krav og behov til en sånn fabrikk.
– Dette prosjektet kan jo ha enorme muligheter?
– Ja, dette prosjektet er veldig viktig fordi det kan bidra til å reduserer utslippene. Derfor har vi et ansvar for å få dette til, avslutter Lea.
SAFEROCK AS
Etablert: 2019
Daglig leder: Espen Lea
Antall ansatte: 10
Omsetning: Ingen
Internett: saferock.no